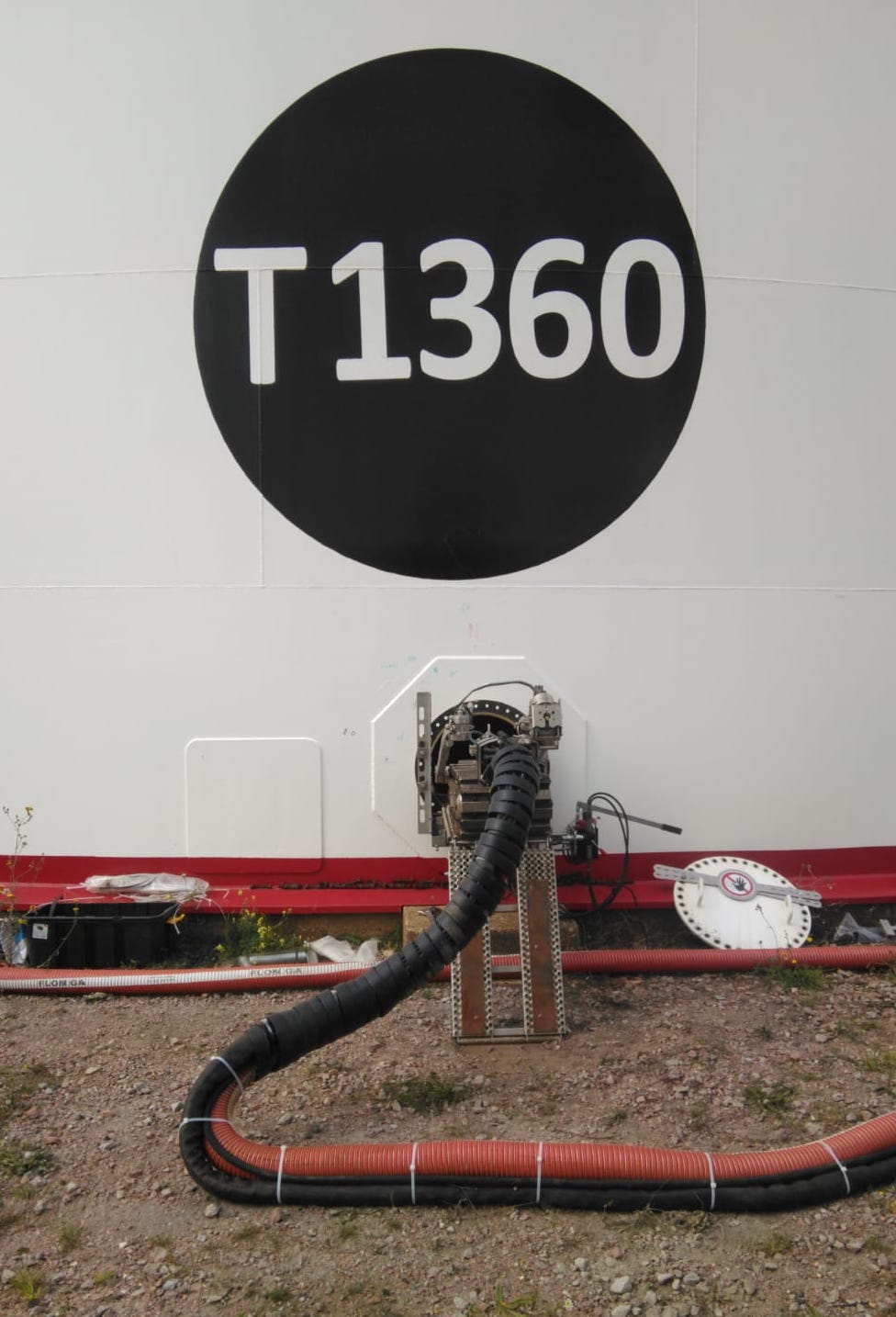
Re-Gen Robotics completes their first crude oil tank clean for Phillips 66 Humber Refinery
Until the launch of 100 % no man entry robotic tank cleaning in March 2019, the only tank cleaning option available to terminal operators was to send personnel inside fuel tanks with highly explosive atmospheres, using breathing apparatus and chemical suits.
Traditionally, people have had to enter oil tanks to implement inspections, de-sludge and clean for product change. Although safety regulations and industry standards are stringent, accidents can occur due to human error and the failure of safety devices.
Exposure to hazardous petrochemicals, heat stress, lack of oxygen, slips and falls, fires and explosions are the main risks faced by personnel who manually clean oil tanks.
Responding to the rising number of confined space deaths and after years of extensive research, Europe’s first and only Zone 0, EX certified company, providing a 100% ‘no man entry’ robotic tank cleaning service was established.
The patented solution ensures workers aren’t endangered by operations carried out in hazardous confined space environments.
Four main robotic tank cleaning services are available to a range of companies across the UK and Europe. These include Fixed Roof, Floating Roof, Heavy Fuel Oil and Coned Floor Tank cleaning. At no time is there a need for human presence in a tank. The operator remains in a Zone 1 control unit where activity is scrutinised through a series of ATEX cameras and gas monitoring equipment fixed to the robot. The entire tank cleaning system can be set up in two hours, which is a fraction of the time required for human crews to prepare to enter a tank. But primarily it takes people out of hazardous spaces, filled with chemicals and gasses that can create serious long-term health issues.
No man entry tank cleaning solutions has very clear advantages for tank terminal operators; there are fixed costs, reduced paperwork and permits, and no requirement for capital outlay or standby rescue teams.
Since 2019, 10,000+ hours of confined space cleaning have been eliminated, leading to an overall reduction in both accidents and health and safety incidents on site. The bar for safety has been raised in an industry riddled with potential dangers and the frequency of injuries and fatalities in the tank terminal sector has been significantly reduced.
CASE STUDY Re-Gen Robotics has carried out the first no man entry crude oil tank clean for Phillips 66 Limited’s Humber Refinery.
Phillips 66 Humber Refinery is one of the most complex refineries in Phillips 66 portfolio and one of the most sophisticated refineries in Europe. The vast range of products it produces includes not only fuel, but raw materials that are transformed into everything from essential components for electric vehicle batteries to toiletries. Some 20 per cent of all UK petroleum products come from their Humber Refinery.
By removing confined space entry, a new era in safety for tank cleaning has been established.
As the exclusive operator of this service, Re-Gen Robotics actively facilitates site visits to demonstrate to potential clients that the service offered is making tank cleaning an intrinsically safer, faster and smarter process.
Following a full demonstration of its service, cleaning a 48m crude oil tank with steam coils, Re-Gen Robotics was commissioned on Phillips 66 Humber Site, to clean a 50m Fixed roof, cone-up floor crude oil (black) tank.
Given the information provided by the client they received a sample proposal on the indicative timings and cost of the tank clean, as exact tank furniture details and volume of sludge were unspecified. The team then visited Phillips 66 onsite, to gain a detailed understanding of the scope of work.
Post site visit, a final proposal outlining method, timeframe, and cost was provided. The tank had numerous steam coils which the robot was required to navigate around. The volume of waste inside the tank was understood to be approximately 135T and the product temperature was ambient.
This was the first ‘no man’ entry tank clean for Phillips 66 and they were pleased at the prospect of eliminating the need for personnel to physically enter their tank to clean it.
The robotic tank cleaning system has an offset suction head to allow meticulous cleaning underneath heating coils and an auger system for the removal of heavy sludge. It boasts front and rear ATEX CCTV and lighting for easy internal tank navigation and inspection. This tool alone can decrease tank cleaning time by 10 to 12 per cent.
Using high pressure, low flow jetting systems and a powerful 4,800 c/m3 vacuum, the heavy oil tank cleaning robotic system was designed to easily fit through a standard 600mm manway, using externally fitted hydraulic ramps.
Robots use up less water that human crews use when cleaning the same tanks. The robots also clean the tanks in half the time that humans do, which all reduces the effect on the environment.
The operator remained in the Zone 1 control unit where he could monitor activity through a series of ATEX cameras and gas monitoring equipment fixed to the robot. In total, 536T of sludge was removed from the tank, with 92T of water utilised during the entire tank clean. Traditionally it would have taken a team of six men 95 days to complete the clean, in comparison with no man entry cleaning, the three-man team took only 43 days i.e., 1,520 robotic hours, to do the job. Thirty of those days were spent on sludge removal alone.
Overall man hours onsite were reduced from 12,160 to 1,032 and the standby rescue team was not required. Re-Gen Robotics is classed as a medium risk contractor therefore less paperwork and permits were necessary, there was also no requirement for capital outlay or spading of the tank, which can take a full day to accomplish.
Upon completion of the tank clean, client feedback was extremely positive. This was the first tank to be completely cleaned and inspected by the company, worldwide, without the need for human presence in the tank.
Following the initial contract, Re-Gen Robotics was commissioned to clean a further three tanks at the site and has recently been included in the tender process for 14 tanks over the next three years. At present the company is 75 percent through their clean on the second of the three tanks.
Phillips 66 has acknowledged the success of the no man entry tank clean because the system could be adapted to suit their individual needs and time frames - a one stop shop for safer, faster, and cost-effective tank cleaning, with measurably better results than the man entry method.
The entire tank cleaning operation was recorded on CCTV from the ATEX cameras and was made available to Phillips 66 upon completion of the works. All files are date and time stamped to ensure the process is traceable for auditing purposes.
A record of gas detection readings was produced by the onboard gas monitoring equipment and issued on completion of the tank clean. The intelligent onboard truck telemetry system collects data that can then be aggregated and analysed to optimise the process. The combination unit provides real time information on all key parameters, which helps monitor energy consumption and waste generation and is vital for both conserving funds and running a cleaner, greener business.
Because hazards relating to tank cleaning are as many and varied as the designs and physical dimensions of the tanks themselves, robotic tank cleaning technology is continuing to be developed at pace so that the equipment can perform more and more tasks remotely.
Rapid technological advancements are powering this new generation of smarter, more mobile, safer robotic tank cleaning systems. They are dexterous and versatile and can navigate and work in their environment using multiple sensors, while their operator remains in an air-conditioned control room, protected from hazardous conditions.
Applying fully integrated, 100% no man entry, closed loop, robotic cleaning technology is where a monumental difference can be made to safety in oil tank industry. Robotic tank cleaning is eradicating industry fatalities and hugely decreasing all risk categories, by eliminating human exposure to confined spaces.
In terms of speed and efficiency, the robotic system on average completes a job 40-80% faster than a manned crew. For example, a white oil tank that would usually take eight days to clean with an eight-person team can now be cleaned in 2.5 days with just two people operating the robot. In manhours terms it has eradicated the requirement for 260 manhours of confined space man entry, carrying with it an enormous safety benefit.
The last two years have been a ground-breaking time for the industry, with respect to Health & Safety. The tank cleaning industry has made a paradigm shift in attitude toward safety.
To date over 30 tanks consisting of white oil, black oil and distillate tanks in gas plants have been cleaned and the first worldwide, 100% ‘no man entry’ tank cleans for oil majors such as Shell, Philips66 and Vermilion have been completed.
These companies have now adopted no man entry tank cleaning as their only preference for tank cleaning and this service now sits at the core of their safety strategy.
Shell has committed to end manned tank cleaning across its operations by the end of 2022, with other majors looking at 2025.
For more information visit www.regenrobotics.com